For range-finding and distance sensing, Time-of-Flight (ToF) is very powerful when emitting light rather than sound.
Compared to ultrasound, it provides far greater range, faster readings, and greater accuracy whilst still maintaining small size, low weight and low power consumption characteristics.
Time-of-Flight (ToF) sensors are used for a range of applications, including robot navigation, vehicle monitoring, people counting, and object detection. ToF distance sensors use the time that it takes for photons to travel between two points to calculate the distance between the points.
WHAT IS THE TIME-OF-FLIGHT PRINCIPLE? - THE BASICS
The Time-of-Flight principle (ToF) is a method for measuring the distance between a sensor and an object, based on the time difference between the emission of a signal and its return to the sensor, after being reflected by an object. Various types of signals (also called carriers) can be used with the Time-of-Flight principle, the most common being sound and light.
TeraRanger sensors use light as their carrier because it is uniquely able to combine higher speed, longer range, lower weight, and eye-safety. By using infrared light we can ensure less signal disturbance and easier distinction from natural ambient light, resulting in the highest performing distance sensors for their given size and weight.
TIME-OF-FLIGHT PRINCIPLE: INDIRECT VS. DIRECT TOF SENSORS
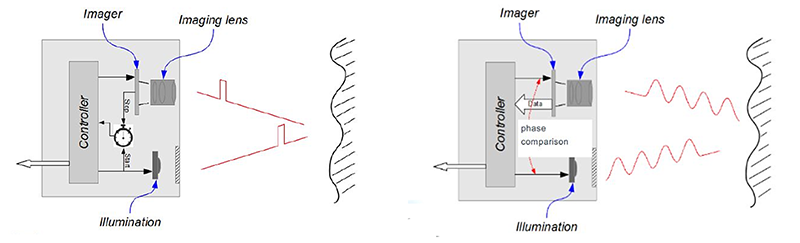
All Time-of-Flight (ToF) sensors measure distances using the time that it takes for photons to travel between two points, from the sensor’s emitter to a target and then back to the sensor’s receiver.
Indirect and direct ToF both offer specific advantages in specific contexts. Both can simultaneously measure intensity and distance for each pixel in a scene.
Direct ToF sensors send out short pulses of light that last just a few nanoseconds and then measure the time it takes for some of the emitted light to come back. Indirect ToF sensors send out continuous, modulated light and measure the phase of the reflected light to calculate the distance to an object.
TIME-OF-FLIGHT PRINCIPLE TECHNOLOGY COMPARISON
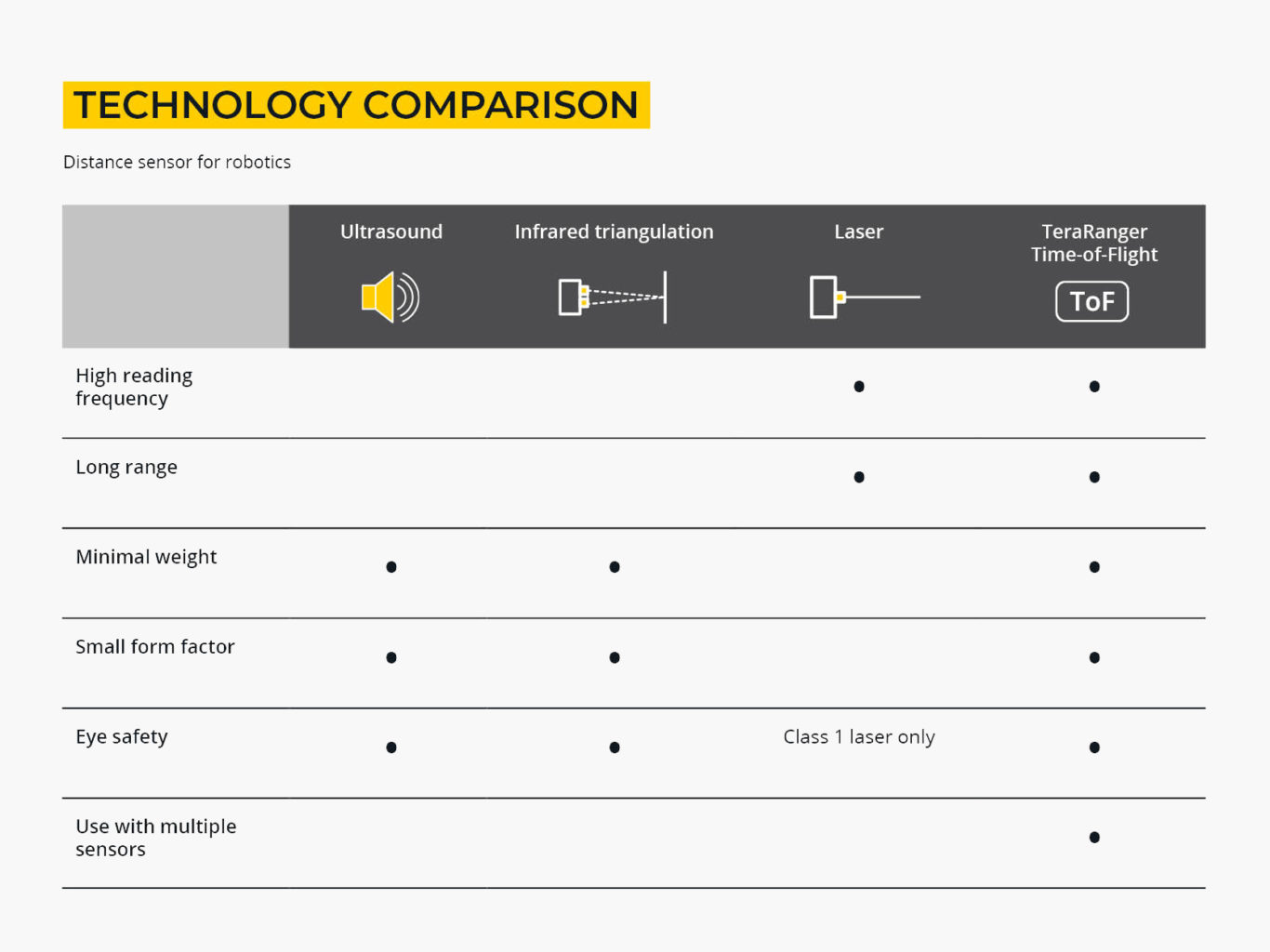
TIME-OF-FLIGHT APPLICATIONS: TIME-OF-FLIGHT PRINCIPLE IN ACTION
Time-of-Flight (ToF) sensors are used for a range of applications, including robot navigation, vehicle monitoring, people counting, and object detection.
ToF sensors in people counting
Conventional imaging systems are great for capturing basic information about an object or a scene but fail to give an accurate impression of distance.
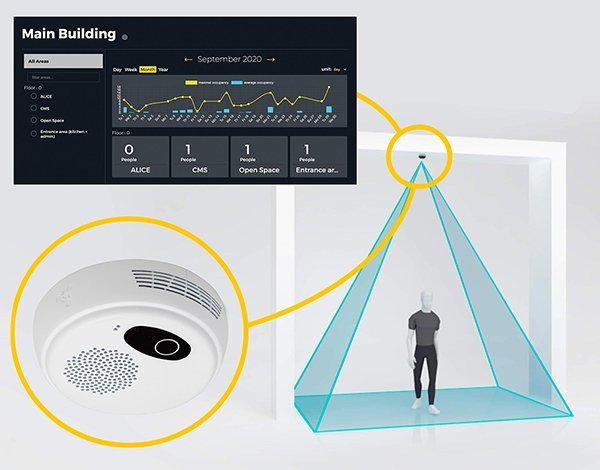
Human perception is such that we can often intuit the depth of field in a photograph and understand – albeit vaguely – how far away the sensor is positioned from the subject. Autonomous systems like people counters and motion detectors have no such luxury. They rely on the Time-of-Flight principle to calculate the distance between a sensing element and the subject/s of interest.
Time-of-Flight (ToF) sensors have proven a revolutionary concept in people counting applications worldwide. With the utmost precision guaranteed and unique considerations in place regarding personal privacy and data protection, ToF sensors enable people counting applications which offer superb insights into a variety of key business metrics, from periodic occupancy counting to space optimization.
TERABEE'S TIME-OF-FLIGHT BENEFITS
Time-of-Flight (ToF) is a powerful technology for accurate, affordable distance and depth-sensing technology.
Small and lightweight
ToF sensors are the small size and light weight while ensuring high performance level (a TeraRanger Evo weighs just 9g!). This means that sensors can be placed in locations not previously possible when using larger, heavier sensors. For smart buildings and level monitoring, this is a real advantage!
Long range
Despite their small size and light weight, tof distance sensors pack a powerful performance punch! TeraRanger Evo can measure distances at up to 60m range. And this is done with LED technology, not a laser! (See section on LED illumination.)
Fast refresh rates
ToF sensors are optimized for high-speed readings. In addition to being small and lightweight, high data refresh rates are central to our design ethos, making the sensors ideal for fast-moving applications, from counting people to industrial automation.
Led illumination
Instead of using laser emitters we use Infrared LED technology. This brings a number of important benefits.
- Eye-safety: TeraRanger sensors remain eye-safe in all conditions, with no need for Laser Class 1 safety precautions!
- Field-of-View: Rather than measuring a very small point, we can allow the emitted light to spread and form a Field-of-View. In many applications, this can be a distinct advantage. Imagine a sensor trying to detect a tree. With a laser, you might detect the leaves, or pass through the gaps and detect something much further away. In a robotics safety or anti-collision situation, this could spell disaster. With TeraRanger technology you are far more likely to detect the hazard you want to avoid. Generally, at 1m to the target, a TeraRanger One sensor is measuring an area approximately 4cm by 4cm.
- Power consumption: Compared to some laser devices, LED’s consume far less power; something all users relying on battery-power will enjoy.
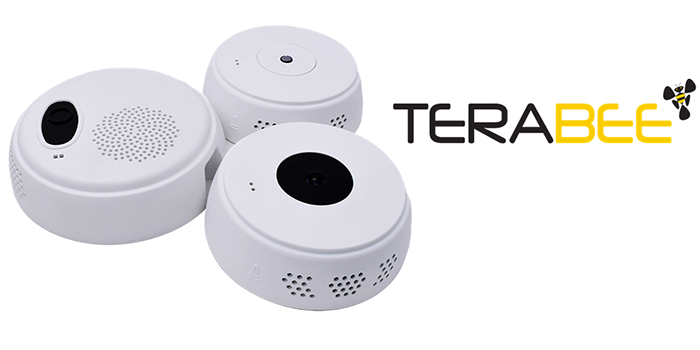
People Occupancy Counting sensor from Terabee
Terabee’s People Occupancy Counting sensor stands out for its cutting-edge features.
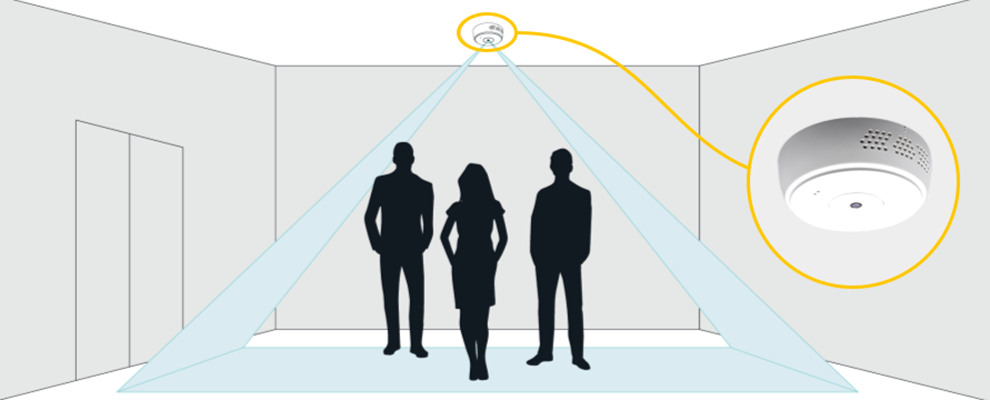
Utilizing advanced thermal imaging, this sensor offers real-time, high-precision occupancy monitoring. With its compact design and easy installation, it seamlessly integrates into various environments, from offices and meeting spaces to reception halls, enhancing space management capabilities. The device can focus on multiple regions of interest, up to eight, to monitor or exclude specific areas.
The sensor’s ability to count occupants accurately without capturing personal identifiable information (PII) ensures privacy compliance, aligning with GDPR regulations and respecting individuals’ rights to privacy within monitored spaces. Moreover it ensures precise occupancy tracking in all light conditions. This is ideal for fine-tuning energy management, optimizing space utilization and automating building operations.
Q&A
Can Terabee people occupancy counting technology be integrated with existing building management systems, and what are the steps involved in this process?
Terabee’s people occupancy counting technology can be integrated with existing BMS. The process typically involves connecting the Terabee sensors to the BMS via standard protocols like Modbus or BACnet. Detailed integration instructions are provided by Terabee, ensuring a seamless integration process.
Are there any limitations or challenges associated with implementing Terabee people counting devices in different types of environments, such as varying lighting conditions or architectural layouts?
While Terabee’s people counting devices primarily use Time-of-Flight and thermal infrared technology, which are less affected by lighting conditions, there can still be challenges in certain environments such as very bright sunlight. Additionally, architectural layouts with obstacles or reflective surfaces may impact the accuracy of the sensors. Terabee provides guidance on sensor placement and environmental considerations to mitigate these challenges.
How does Terabee ensure the privacy and security of the data collected through their people occupancy counting technology, especially in light of increasing concerns about data protection and privacy regulations?
Terabee ensures privacy and security by designing their sensors to collect only non-personally identifiable information (PII) through thermal infrared technology and Time-of-Flight technology. This means that the sensors do not capture images or any identifiable features of individuals, thus eliminating privacy concerns associated with traditional camera-based systems.
How easily can Terabee’s people occupancy counting system scale to accommodate buildings of different sizes and layouts? Are there any limitations in terms of the number of sensors that can be deployed or the coverage area they can effectively monitor?
Scalability and flexibility of Terabee People Occupancy Counting: the people occupancy counting sensor is designed to be highly scalable and flexible to accommodate buildings of various sizes and layouts. The system can easily scale by adding additional sensors as needed, and there are typically no limitations on the number of sensors that can be deployed within a building. Additionally, Terabee offers people flow counting sensors with varying coverage ranges to suit different space requirements, ensuring effective monitoring across diverse environments.
What kind of maintenance and support services does Terabee offer for their people occupancy counting devices? Are there any ongoing calibration requirements or software updates needed to ensure accurate and reliable performance over time?
Terabee provides comprehensive maintenance and support services to ensure the long-term performance of their people occupancy counting devices. This includes firmware updates to ensure compatibility with the latest technologies and security standards. Additionally, Terabee offers technical support and troubleshooting assistance to address any issues that may arise, ensuring uninterrupted operation and maximum uptime for their customers.